Emulsion mist separator
MultiCNC
Emulsion mist separator for turning, grinding and milling machines.
The new oil emulsion mist separator from Hengst removes cooling lubricant mist from the contaminated air in metal-cutting machines. The device generates a slight negative pressure in the machining area of the machine and thus prevents the excessive escape of cooling lubricant aerosols during operation and when the doors are opened. This significantly reduces the pollution in the entire hall. The three-stage filtration is optimally adapted to cooling lubricant aerosols and supports compliance with the limit values in accordance with DGUV 109-003.
Thanks to the highly efficient EC fan, energy consumption is significantly lower than that of most comparable devices. The first filter stage, which can be cleaned several times, also contributes to lower operating costs. A safety mechanism / "anti-shear" mechanism protects the gasket of the main filter during installation.
*On request, the separator is also available up to filter class H13 and with 400 V supply voltage.
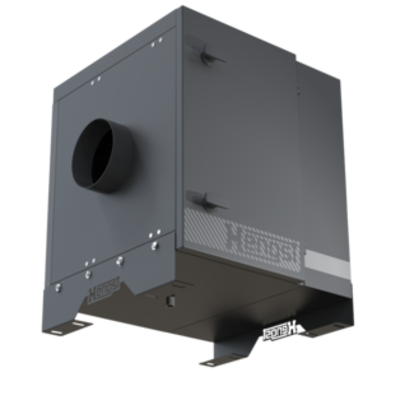
Benefits
MultiCNC – Your customer benefits at a glance:
Available from stock
Made in Germany
Benchmark in terms of energy efficiency
Quick & tool-free filter change
3-stage filtration
Protective mechanism for the main filter Gasket
Product variants
![]() | ![]() | |
Model 1200S
|
Model 600S
| |
Connected load | 500 W | 169 W |
Nominal volume flow | 1,200 m³/h | 600 m³/h |
Filter class | ePM1 80% | ePM1 80% |
Supply voltage | 230 V / 50 Hz | 230 V / 50 Hz |
Dimensions (H/W/L) | 580 x 500 x 685 mm | 580 x 500 x 625 mm |
Weight | 33 kg | 28 kg |
Emulsion mist | ✓ | ✓ |
Oil mist (moderate concentration) | ✓ | ✓ |
Tool-free filter change | ✓ | ✓ |
Anti-shear for filter seal | ✓ | ✓ |
Differential pressure monitoring | optional | optional |
Air flow adjustable | optional | optional |
FAQ
What dangers do cooling lubricant vapors pose?
Cooling lubricants can contain a whole range of different substances. These include biocides, for example. Employees are permanently exposed to these substances. The concentration of oil mist and emulsion mist in the air must therefore be reduced to protect health.
What is oil mist extraction?
An oil mist extraction system is a filter system that extracts cooling lubricant vapors from the machining areas of machine tools. Cooling lubricants usually contain oil. The oil can also be the basis of the coolant lubricant (non-water-mixed coolant lubricants). In the majority of applications, however, it is present as an emulsion mixed with water.
Which filter class does an oil mist extraction system require?
The average particle size in relation to the mass is approx. 1.5µm to 2.5µm. For various grinding processes, it is even higher. With an ePM1 80% filter (according to ISO 16890), aerosols of this size are filtered out for the most part. Higher filter classes may be indicated if critical materials are processed whose particles are to be additionally filtered. With minimum quantity lubrication, the particle size is somewhat smaller. A higher filter class is therefore sometimes used here.
How is the filter efficiency of oil mist separators standardized?
ISO 16890 is usually used. The standard determines the efficiency for atmospheric aerosols whose fine fraction peaks at approx. 0.3 µm. This is significantly smaller than is normally the case with cooling lubricant mist. The actual ePM1 efficiency for coolant filtration is therefore significantly higher than the standardized classification value. EN779 is no longer valid for classification. Sometimes HEPA filters are also used, which are standardized by EN 1822 and the very similar ISO 29463. These standards determine the efficiency for the so-called "Most Penetrating Particle Size" (MPPS), i.e. the particle size that can be filtrated the worst by the filter.
Is the Hengst MultiCNC also available with a HEPA filter?
HEPA filters are also available for the Hengst MultiCNC and can be easily retrofitted. When retrofitting, the standard Lotex 1704 pre-filter mat should also be replaced with a Lotex 1805 pre-filter mat in order to achieve a longer service life for the HEPA filter. These filter mats are already included in the HEPA filter set. As the pressure losses are higher when using this filter combination, the Air flow is reduced by approx. 100m³/h when new.
Is the MultiCNC suitable for my application?
The MultiCNC is designed for a very wide range of applications. With normal concentrations and proper extraction of cooling lubricant mist (see also the further information here in the FAQ), very long filter service lives are achieved. The MultiCNC also works reliably at higher concentrations. The only thing that needs to be ensured here is that the filters are replaced more regularly. The filter principle of the MultiCNC shows its strengths particularly when using emulsions, but light applications with oil mist can also be handled very well. Further information on the concentrations of coolant mist that can usually be expected can also be found in DGUV Rule 109-003 Annex 1.3.
Can an oil mist extraction system be retrofitted?
The Hengst MultiCNC can be retrofitted very easily. Many existing systems do not yet have a filter unit. As the device is then not included in the machine manufacturer's CE declaration of conformity, it is a complete machine in accordance with the Machinery Directive and is supplied with its own CE marking and a mandatory main switch with emergency stop function.
Where do you install an oil mist extraction system on the machine tool?
The Hengst MultiCNC can often be mounted on rails and vibration dampers on the machine housing, or on a small stand next to the machine. The simplest connection is via a suitable flexible hose. Ideally, the device should be positioned above the extraction point so that coolant can flow back out of the extraction hose if necessary.
How should the extraction point of an oil mist extraction system be designed?
The extraction point should be as far away as possible from the actual machining area to prevent the direct entry of coolant spray and chips. On lathes, for example, the opposite side of the lathe chuck is often well suited. A metal mesh is ideal at the connection point of the extraction system to keep out coarse dirt. However, this must be cleaned regularly to prevent clogging. If it is foreseeable that this will be difficult to ensure, a baffle plate should at least be provided in front of the extraction point to catch coarse particles. If you have any further questions, please do not hesitate to contact us.
How do you monitor/check the filters of an oil mist extraction system?
Many oil mist separators work very well without instruments to monitor the filter condition. If the filter load is too high or the extraction point is blocked, this is indicated by noticeably reduced air volumes. Alternatively, a pressure gauge can monitor the pressure differences between the filters. Optionally, a differential pressure switch can also be used to send a message to the machine tool. In any case, checking the filter should be included in the machine's maintenance schedule.
How is the Hengst MultiCNC electrically connected?
The connection diagram can be found on the product page. Basically, the MultiCNC only requires a 230VAC power supply with the appropriate power (170W / 500W). In the simplest case, the device can then be switched on at the start of the shift using the main switch included and switched off again at the end of the shift. If required, the power of the fan can also be controlled via a potentiometer, a 0...10V input or pulse width modulation (PWM).
What is a sensible control system for oil mist extraction?
If the aim is to control the Hengst MultiCNC, it would make sense, for example, to reduce the power slightly when the door to the machining area of the machine tool is closed. If the door is opened, the machine should be run up to full power immediately in order to protect the machine operator as well as possible from escaping cooling lubricant vapors. If the door remains open, the MultiCNC can also be set to "0" after a certain time. The run-on time should be carefully considered, as the device also has an effect on subsequent processes, such as blowing off the workpieces with compressed air.
Downloads
726 KB
325 KB
545 KB
2 MB
196 KB
121 KB